
Digital Creation of the Future
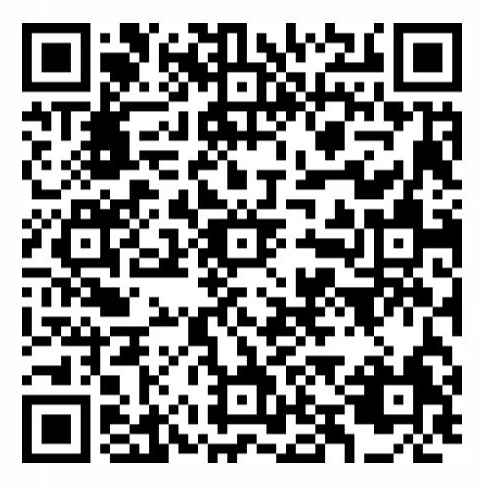
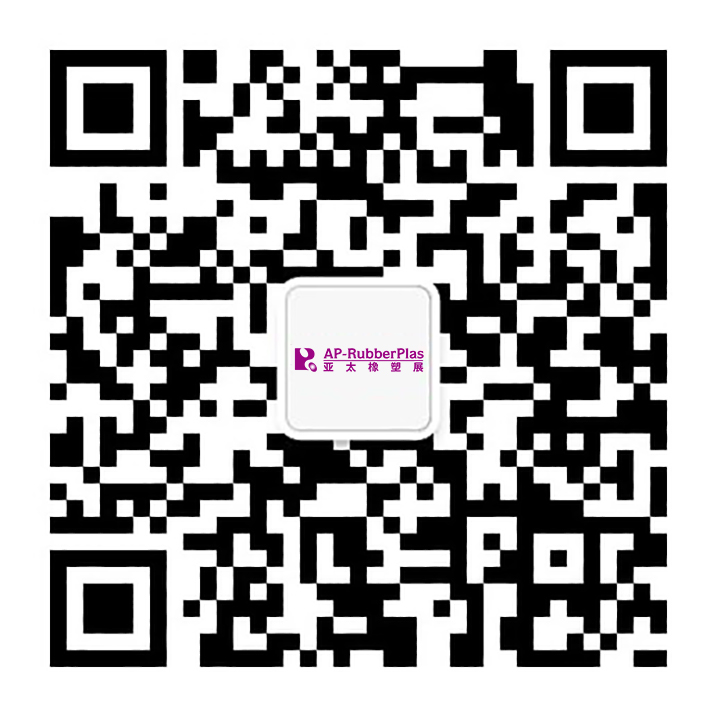
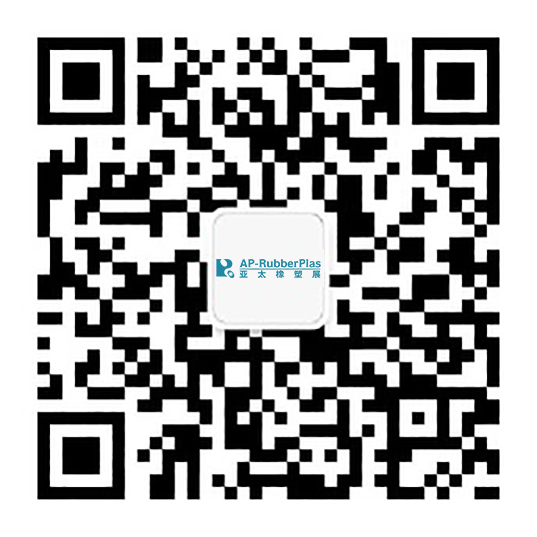
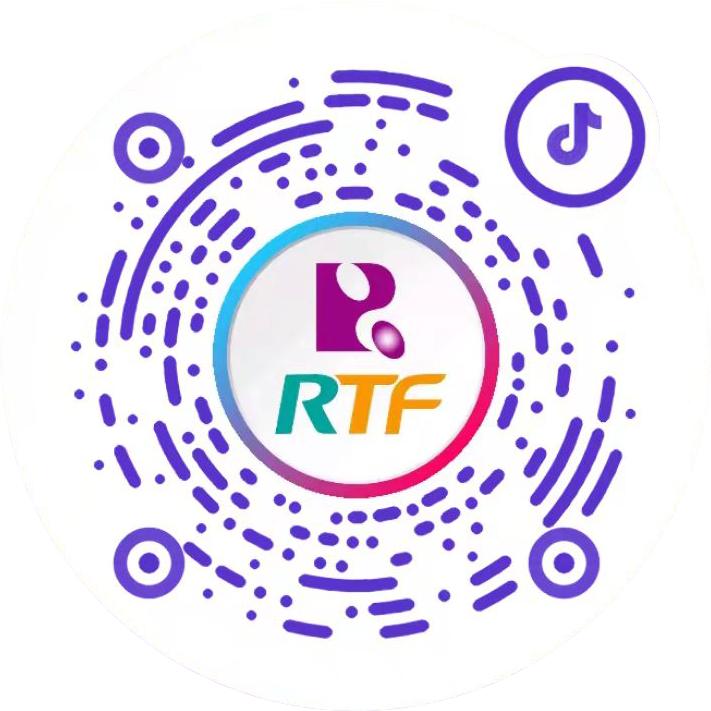
配方和原材料选用
配方中橡胶、炭黑及助剂的品种、性能和用量的制定是否恰当直接影响胶料的塑性值和焦烧时间, 从而影响着橡胶制品外观。
混炼密炼
密炼过程中胶料塑性值偏低、流动性差 、粉料分散不均匀、炼胶温度过高及返炼时辊温过高导致硫化点提前和焦烧时间缩短等都有可能导致缺胶现象的产生。
硫化
硫化前胶表面粘有油污或脏物未清理干净、胶外喷涂不均、模具不洁 、混炼胶存放时间过长或者存放处室温过低 ;隔离剂涂刷过多且不均匀及模型上的水未吹干净胎坯即装入模型中硫化 ;硫化时温度升得过快 ,硫化期间内压不足;模型排气孔堵塞等也可能造成缺胶。
模具设计
设计中材料分布不合理或胶用量不足 排气孔和排气槽分布不合理等也有可能造成缺胶。
加工工艺
加工工艺不合理也能导致缺胶现象的产生。
总结:
因主要有:
半成品单耗不足或装胶量不足;
平板上升太快,胶料没有充分流动;
模具封不住胶料;
模具排气条件不佳;
模温太高;
配方和原材料问题等等;
加工工艺控制不好,焦烧段。
可以从这些方面解决:
从新确定模具装胶量;
减慢平板上升速度并反复放气;
改进模具设计;
降低模温,加快操作速度;
降低模温;
修改配方和模具等。
适当控制加工工艺,提高胶料焦烧时间。
附橡胶制品常见的质量问题:
一、缩边现象
(1)硫化温度太高
(2)胶料过多
(3)硫化速度太快
(4)开溢料槽没有
(5)模具问题
缺料原因:
(1)模具与橡胶之间的空气无法排出
(2)称重不够
(3)压力不足
(4)胶料流动性太差
(5)模温过高,胶料焦烧
(6)胶料早期焦烧(死料)
(7)料不够厚,流动不充分
解决:
(1)加开排气槽
(2)多排气
(3)提高压力
(4)改配方,增加胶料流动性
(5)改配方,延长焦烧时间
(6)增加料厚度
二、喷霜,发白
原因:
(1)硫化不足.
(2)配合剂过量,超过橡胶的溶解度.
解决:
(1)延长硫时或采取二次硫化
(2)调整配方,减少低溶解度
(3)配合剂的用量
三、气泡、发孔
原因:
(1)硫化不足
(2)压力不足
(3)模内或胶料中有杂质或油污
(4)硫化模温过高
(5)硫化剂加少了,硫化速度太慢
解决:
(1)加压
(2)加长硫时
(3)调整配方,加快硫化速度
(4)多排气
(5)模温不能过高
(6)增加硫化剂用量
四、重皮、开裂
原因:
(1)硫化速度太快,胶流动不充分
(2)模具脏或胶料粘污迹
(3)隔离剂或脱模剂太多
(4)胶料厚度不够
解决:
(1)降低模温,减慢硫化速度
(2)保持胶料.模具清洁
(3)少用隔离剂或脱模剂
(4)胶料够厚
五、产品脱模破裂
原因:
(1)模温过高或者硫时过长
(2)硫化剂用量过多
(3)脱模方法不对
解决措施:
(1)降低模温
(2)缩短硫时
(3)减少硫化剂用量
(4)喷脱模剂
(5)采取正确的脱模方法
六、难加工
原因:
(1)产品撕裂强度太好,(如高拉力胶)。这种难加工表现为毛边撕不下来。
(2)产品强度太差,表现为毛边很脆,会连产品一起撕破。
解决措施:
(1) 如果是撕不掉,就得调整配方,多填充配合剂,减小收缩率。
(2)如果是撕破,a降低模温,缩短硫时;b减少硫化剂用量;c调整配方,增加胶料强度。
下面以硅胶为例,仅供参考:
硅胶制品在生产过程中出现缺胶现象基本上是屡见不鲜,造成材料短缺的产品不计其数,但由于这一现象属于后加工问题,对于模具和原材料都没有涉及到这两个环节,所以,可以说,这种情况的主要收入往往是人为因素造成的,如果缺胶的主要原因仍可分为多种类型,那最重要的就是硅胶制品制造商在生产和加工过程中的细节控制问题,因此,摸索和探索加工工艺是重要的!所以,总结了以下原因,包括缺乏胶水和材料的现象。
1、 橡胶精炼完成后,没有准确的切割工序,原料的重量不够。
2、在产品打样期间没有准确的模具测试,原材料的规格和尺寸以及放置方法都没有得到很好的试验,导致由于原料没有填充在模具腔中而导致胶的缺乏!
3、混合后放置原料的时间太长,导致流动性能下降,固化剂失效,无法正常形成!
4、在操作过程中没有放样标准。这一现象通常导致材料和胶水不足占大多数,操作人员对产品不熟练,造成原材料放置不准确,无法流向模具芯的边缘和角落。
5、机器压力太小,通常对于一个相对较厚的孔较小的模具,压力太小很可能导致完全硫化,根据产品的大小进行压力分配!
6、模具温度过高,复杂产品的结构和形状各不相同,这种产品在高温的情况下,化合物在完成浇筑前已经烤熟,这种现象是由高温引起的!
7、对于尺寸比较复杂的产品,表面材料的需求量过大,导致原材料无法充入模具腔,造成材料不足,可以采用不同的方法和方法在模具测试期间对模具进行测试,那是最简单、最有效的方法!